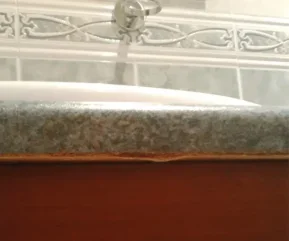
On my travels, I sometimes find myself seeing all sorts of failures in wood panels and furniture. Most often this is connected to using MDF joinery for bathroom installations, or poor laminate design on particleboard fittings, and putting kettles in fitted cupboards ‘out of the way’. This put me in mind to continue considering the key parameters used to test wood panels. This month let’s consider thickness swelling in water.
We know that some panels are required to have higher resistance to water and humidity than others. P3 particleboard for humid environments has a tighter expectation than P1 for general purpose dry applications, for example. For P5 and P7 the requirements are even tougher. But how does this get measured?
The first test is likely to be the thickness swelling test, or BS EN 317 Particleboards and fibreboards. Determination of swelling in thickness after immersion in water. A very similar method is given in ANSI A208.1–2016 for American markets.
The EN 317 standard uses 50 x 50mm sample blocks – the same size as the internal bond test (see previous issue). These are submerged in water for 2 or 24 hours and the level of swelling is evaluated. Care is taken to keep the temperature of the water within the allowable range, and not to artificially constrain the samples preventing them from swelling as they take up the moisture. The measurement should be taken at the centre of the square sample, so a micrometer is usually used to measure a point at the centre of the block, rather than digital callipers which would measure the edges.
The most common version is the 24 hours soaking and a good board should show relatively small change in dimensions. For example, for P3 particleboard of up to 13mm, a change of 14% is the maximum permitted. For dry process fibreboards (MDF) the target is 12%. In practice, for example in joinery products in a bathroom, 12 to 14% would be quite a large dimensional change – and enough to cause some visually detectable change in the quality of the appearance! But P3 is a panel type which is recommended for humid conditions, not for direct immersion in water. In the example that I saw (as shown in the picture) the failure of the particleboard due to water splashes near a sink probably happens in many homes as well as the hospitality sector. Some companies even laminate a special extra distance across this zone to inhibit drops accumulating and causing problems. A higher quality panel might have used different resin and potentially waxes to deter water uptake, but repeated wetting by zealous cleaning staff might still lead to issues developing.
But why do panels swell when they take up water? This goes back to the press process. In the press, the heat cures the resin – yes – but the heat and steam also allows the wood fibres or particles to deform and compress into a compacted arrangement. The panel that exits the press is several times thinner than the mattress that went into the press. The cured resin bond is permanent, but the deformation of the chips and fibres is temporary. Just as the presence of steam with the heat permitted the compression, the presence of water will allow the wood polymers to regain their original shape as they adsorb water. Given enough water (full immersion) or repeated cycles of wetting and drying (like the cleaning situation in the example) the wood will regain a considerable amount of its original dimensions – as far as the resin bonds will permit.
For really high-performance panels, where wetting is more likely (such as those destined for kitchens and bathrooms) an even tougher test would be used. This is the boil test or BS EN 1087-1. This is a far better indicator that a panel will withstand wetting in service, but only intermittent wetting. If you are seeking full resistance to moisture, it is worth considering boards made from modified wood, such as the acetylated fibres in Tricoya MDF which has very low thickness swelling values indeed.