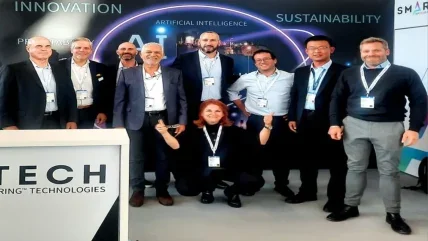
Cost saving is a big focus area for woodbased panels manufacturers due to the current high prices of wood raw materials, chemicals and energy.
In Israel, SMARTECH has been offering a solution to optimise the wax and resin application process to do just that.
In a relatively short time – just eight years in fact since its first commercial systems were sold – the company has over 20 customers in the wood-based panels industry, with almost 50 installations globally.
So what is the system and what has prompted its growth?
The company’s SMARTWAX system is designed to transform the way wax is used. It transforms the wax material into a waterbased wax suspension, that replaces more expensive wax emulsion, bulk solid or slack wax alternatives. The system is integrated directly into existing production lines.
Hanoch Magid, SMARTECH CEO, explained the company’s progress, which started with a thorough examination of the woodbased panels industry. He found a lack of innovation for a variety of reasons.
“When you visit manufacturers you often find them operating with low profit margins and the majority of costs going into raw materials – as much as 50%-60% of the final product – as well as inefficient operations,” he said.
“In order to avoid interruptions in the sensitive production process, they continue to work the same way for years, with very slow steps of improvement.
“Then you have the machinery, the personnel, maintenance and energy. We decided to focus on the most critical and significant areas, optimising the processes and reduction of raw materials.”
SMARTECH realised that it could save 15- 35% of the cost of the raw material, which of course is a huge number in manufacturing.
“We started with the wax, adapting a solution from another industry – the gypsum sector. We have a suspension solution where we mix the wax with water in line, heating it to 60-80O. You create a thin droplet of water with a droplet of wax inside.
“By doing this you manage to optimise the way wax is distributed on the woodchips, which in turn greatly improves the absorption of wax into the wood, creating significant savings on the quantity of wax needed.”
Mr Magid said existing methods currently used in the market are slack wax, paraffin or emulsion.
The latter is wax mixed with water and chemicals offsite and shipped via container to the plant. But he said this not only involves preparation and transport costs, you are also delivering water to the mill, which he says isn’t necessary.
Compared with the regular method of using wax – whether paraffin, slack wax or emulsion – SMARTECH estimates savings of 25-35% on quantity or cost.
SMARTECH’s system is located on the production line and has a small footprint of 5m long x 2m wide. It involves piping wax and water from separate storage tanks into a mixer, where a control system optimises the mixing ready for use in board production processes.
“Our commitment is to meet or do better than customers’ existing systems,” added Mr Magid. “And of course at a significantly lower cost due to the technology.”
We asked SMARTECH what the impact was on speed and efficiency of production.
The company says speed of production can be quicker, as adding water to the process can result in faster and more stable operation of the press.
It recently received an additional order from Egger Group to deliver four additional SMARTWAX Systems in 2023 with an option for four supplementary systems in 2024.
This order continues the long-running relationship between the two companies. Egger currently operates several SMARTWAX Systems at select facilities in Europe.
SMARTRESIN SYSTEMS
It’s not just wax where SMARTECH is innovating for wood-based panels producers.
Its solution is also targeted at transforming MDI and PF resin, the former in real-time to a water-based aqueous suspension with a controlled droplet size and the latter with dynamic thermal control without any additional materials.
According to Mr Magid, this solution for MDI resins – SMARTMDI – is a significant improvement in resin distribution upon the wood substrate and improves MDI reactivity.
“The outcome is a better performance while obtaining significant resin cost savings of at least 15% to manufacturers,” Mr Magid explained.
“We are working with MDI/PMDI and PF. We are currently implementing our first system in the US – one of the big companies that already implemented our wax solution.”
Mr Magid says the customer is an OSB producer.
Existing North American customers, particularly for OSB production, include the largest, market-leading producers. SMARTECH’s installations also extend to Brazil, India, Bangladesh, China and Turkey.
All these customers are using the system for either OSB, MDF or particleboard.
European and South-east Asian customers are mostly related to MDF and particleboard production.
“In the beginning, customers were reluctant to give recommendations about our solution. It seems they wanted to maintain their technological advantage as long as possible,” Mr Magid said.
“Now it is easier and companies are willing to partner in our PR work. Every company starts with one mill, then rolls it out to their other mills. They start with wax and then go over to resin.
“We are giving the operator the ability to mix their preferred wax and resin. It is a better solution for them and they control the process.”
One of SMARTECH’s wax/resin industry partners in Canada is promoting the SMARTECH system as a way of penetrating the market further with an enhanced proposition.
Matt Zarek, SMARTECH business development manager, said the timing was very good currently for its MDI system.
“MDI is not like PF and UF where you can build a resin plant and make it yourself.”
“There are five manufacturers of MDI globally who have 90% market share and to make a world class plant can take a couple of billion dollars and a few years.
“The panels business is at the bottom of the food chain and it gets the low end of the MDI variants.
“The MDI producers want to push up the value chain and provide more value added MDI, which usually means other industries. So our panels sector clients are under pressure with high prices and tough availability.
“Some customers have had to curtail production sometimes over the last two years because of low supplies of resin. A lot of the pricing has gone up for MDI over the last two years – at least double.
“So we don’t need to make a hard claim to get people interested in our MDI solution, as they can drop their costs by 15%.”
Another complication for MDI, which is popular for high quality OSB production, is its exposure to natural gas price fluctuations because of the feedstocks. Of course, it can be unpredictable and it’s tough to run a big panels plant with unpredictable supply.
AUTONOMOUS MANUFACTURING SOLUTION AI-BASED SOFTWARE
It’s not only wax and resin that SMARTECH has turned its attention to – it is efficiency of the entire wood-based panels plant.
Five years ago it began examining production flow optimisations and realised that data was not being fully utilised.
“Because we know how machinery and processes work, we decided to go into the arena of data and artificial intelligence to optimise production processes and flow,” explained Mr Magid.
Backed by real-world manufacturing process experience and expertise in AI and machine learning, SMARTECH developed data-driven solutions for the panels sector.
Its Autonomous Manufacturing AI software solution is designed to aggregate production data and human operator inputs to construct a powerful AI engine to optimise critical production processes.
The software connects to the plant OT/ IT stack and synchronises performance between machines, processes and operators in real-time and pushes process setpoints direct to critical production equipment.
After a short learning period, the tool runs AI algorithms in real time and presents optimised equipment setpoints to the operator for higher throughput, better quality and with greater stability.
The AI tool serves either as decision support for operators or, when in autonomous mode, to autonomously control operations directly with no human intervention.
Its first application was on a small OSB press. SMARTECH installed its software and collected sensor information from machinery and the control room. After three months the solution gave recommendations for the best way to operate the press.
“We checked it and then transferred to autonomous mode and the software controlled the press itself with about a 10% improvement in production,” said Mr Magid.
SMARTECH is partnering with Siempelkamp on the venture, with the latter marketing it as ProdIQ – SmartPress, an autonomous process control for the woodbased panels industry.
The solution will be featured at the Ligna show by both companies.
“We are looking for it to be installed now in select companies around the world,” added Mr Magid.
“It’s an important move [the collaboration with Siempelkamp] because it’s not just a solution which has been recognised by one of the leading technology companies in the industry. It also represents a distribution partnership.”
In conclusion, SMARTECH has made a huge amount of progress in the wood-based panels sector, no doubt due to its long years of R&D preceding the first installation of its SMARTWAX system.
“We are positive about the future because we offer customers value based on cost savings,” said Mr Magid.
“Although not a large company, we have a well-established platform ready to scale up as we grow our marketing and sales activities in the wood panel industry, and also expand into the pulp/paper sector,” Mr Magid said in conclusion.
“We are certainly positive about the future, because we offer customers significant and proven value based on cost savings and operational optimisation.”
Clearly, whatever the general world economic conditions, greater efficiencies and cost savings are an attractive proposition for all manufacturers.