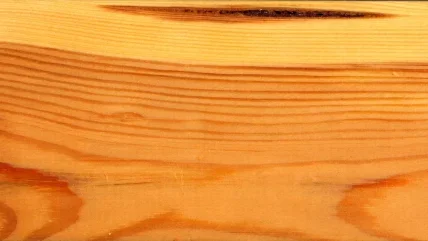
Softboard (aka low-density fibre board, insulation board) may not be the first type of wood based panel to spring to mind, especially when compared with the success of OSB, MDF and particleboard. However, in the last few years softboard has seen a steady increase in production. In Europe during 2017 and 2018 there was a 6-7% increase in production of softboard whilst hardboard and MDF conversely have seen either low growth or a drop in production. Softboard is wet formed, then pressed and dried, somewhat akin to paper making.
This produces a material that doesn’t use adhesive resins, instead relying on the natural components of the fibre, such as lignin, or hydrogen bonding between fibres to bind the boards. It generally has a density in the range from 230kg/m3 to 450kg/m3 and is therefore a relatively low weight product.
Softboard exhibits good thermal and acoustic insulation properties and is therefore routinely used in construction as insulation panels. The board may also provide dynamic buffering of moisture. Conversely the strength properties of the boards are obviously lower than most other types of wood based panels.
So why is softboard increasing production? The move to energy efficient buildings for the past few years is an obvious reason for this gain in popularity for construction.
Acoustic insulation is also clearly desirable for high density housing. Also, the lack of resin binders gives softboard the advantage of extremely low (or zero) formaldehyde and/or TVOC emissions.
As the push for improved air quality in the indoor environment has taken a step forward there has been an impetus for low emission products. Softboard would therefore seem a good candidate for the role. In terms of standards there are a number that are designed for softboards and stipulate its usage, testing and labelling. In Europe EN 622-4 and EN 316 specify the requirements for softboard, whilst in America that is detailed in ASTM C208-12. Testing of boards is detailed in EN1058 and ASTM C209. Other standards such as insulation value and fire testing standards are also applicable.
The future innovation for softboard may rely on process improvements in dewatering, and reduction of the energy and time required to dry the boards. The use of both non-virgin wood and nonwood lignocellulosic material is already a feature of the industry; further research and innovation make this an interesting and developing area to observe.
The use of recycled fibre in particular is one that shows great promise and fits very well with sustainability targets and reducing the loading on land fill. The prospect of reuse and recycling of softboard should be easier than with other types of fibreboards, as they lack the resin of other fibreboards.
Alongside the development of the fibre furnish there are also exciting prospects in the improvement of physical properties with innovative additives. The aim is always, of course, to maintain the good thermal, acoustic and low emission profiles intact, but there are advances to be made in this area. Aside from the mechanical and insulation properties of the boards, additives may also enhance other very useful and exciting characteristics of the fibre, for example, to improve the moisture buffering and to reduce any susceptibility to mould growth.
Various additives, such as minerals or nut shells, that have been used in medium density fibreboard to not only reduce VOC emissions but also actively scavenge those VOCs from the interior environment should also be applicable to softboards.