Leverkusen, on the northern outskirts of Cologne in western Germany, has been home to Schenkmann & Piel (SPV) since October 1, 1977 when two partners founded the business with a one-product portfolio.
That product was an air grader, or air sifter, targeted on the particleboard industry. Today, in addition to those graders, the company offers a variety of dryers for particleboard, OSB and MDF factories, supplying complete systems with all necessary controls and ductwork.
The company is not, and never was, a large manufacturing operation but concentrates on the design and development of products which are largely made by approved sub-contractors with a long experience of working with SPV.
Exceptions to this are the key components of the graders and dryers which are manufactured in SPV’s own workshops; there is no point in transporting ducting half way round the world when it can be fabricated locally at lower cost.
A major change for the company came in 1999 when press and complete line supplier Dieffenbacher of Eppingen, Germany, took a 20% share in SPV. The two companies had worked closely together for some years and so the ‘marriage’ was in a sense a natural one.
One of the founding partners of the Schenkmann & Piel business, Fred Schenkmann, retired in October 2001 and was succeeded by Peter Wolff as general manager. Mr Wolff has considerable experience of the panel industry, having formerly been in charge of sales for press maker Küsters, now part of the Metso Panelboard group.
But back to products and that original air sifter which proved a good foundation for SPV as the company can now boast sales of more than 2,500 units.
Originally, the purpose of the sifter was to remove oversize particles from a pretty clean raw material, but times change and so has particleboard furnish – in some cases dramatically. Thus SPV’s sifters are now more likely to be required to deal with a wide range of contaminants in recycled wood.
Italy has been a particularly strong market in this respect as virtually all Italian particleboard mills use exclusively ‘urban’ wood supplies.
Recent sifter installations by SPV include the Glunz (Sonae group) mill at Nettgau in Germany and Egger’s mill at Rion des Landes in France.
The air grader splits the incoming material into two fractions: accepts and heavyweight rejects. In the process, 85% of the air used is recirculated to reduce dust emissions, while the balance is cleaned before venting to the atmosphere.
Inside the air grader, the material enters via a rotary valve and central tube. Rotary arms then distribute it uniformly over a perforated plate through which air is drawn.
Separation is effected by differing air velocities, with the heavier fraction moved to the edge, exiting via an air lock. The lighter fraction is separated from the air stream by high-efficiency cyclones known as Hurriclones.
This grader system can be used to separate core and surface material (the SR Grader), or to separate out pollutants where recycled wood material is being used (the SR-R Grader).
The company also offers its Heavy Goods Air Grader SGH for contaminated wood supplies. In this version, the incoming material is split into two fractions: accepts and heavy weight rejects. The rejected material drops into the reject hopper and is discharged from the system, while the acceptable material is carried in the air stream to a high-efficiency Hurriclone. In this system, up to two thirds of the air can be recirculated.
For fibres in MDF and hardboard plants, SPV offers the SGF air grader which again separates the incoming material into two fractions, with reject material such as glue balls, wood shives and sand dropping into a reject hopper. Acceptable material is transported in air suspension to a high efficiency cyclone and the exhaust air is cleaned in bag filters. Up to 60% of the cleaned air is recirculated.
Sand is a major problem in particleboard mills using recycled wood as it is highly abrasive and can also cause severe problems in the dryer. A combination of mechanical screening and pneumatic grading is employed by SPV for sand extraction.
Sand particles of less than 300 micrometres are taken out by screening over a 1.2mm and a 0.3mm mesh. Material retained on the 0.3mm mesh is air graded to remove sand particles between 300 micro-metres and 1200 micro-metres, which are separated from the accepts stream. Material retained on the 1.2mm mesh screen is usually free of contaminants, says SPV, and can be used in production. The company claims that 80% of sand can be removed in this system.
Following on to its success in the grading arena, some years ago SPV moved into dryers for composite panel factories and offers single-pass drum dryers for particleboard and OSB, and flash-tube dryers for MDF.
The drum dryers employ indirect heating with heat exchanger tubes, or coils. The drums are virtually air-tight and have thick walls for insulation. They are driven by electric motors through a pinion system to a ring gear. Dryers with capacities of up to 65,000kg per hour mechanical throughput are available.
Drum dryers have been supplied to many mills around the world and recent installations include some large diameter drums to Saviola in Italy and drum dryers are currently under construction for Kronospan in Russia and Falco in Hungary.
This year, flash-tube dryers have been supplied to Homanit’s MDF plant in Mount Gilead, North Carolina and the Kunz plant in Baruth in eastern Germany.
China has also been an important market for SPV, with three plants currently on order for flash tube dryers and sifters for Gao Feng, Oak and Zenghe – all obtained through Dieffenbacher as the main contractor; the source of about 50% of SPV’s business in the last two years.
The flash-tube dryer employs a singlestage system which reduces the moisture content to around 10%.
For pneumatic transport and extraction installations, SPV offers its Rotaclean Filter. This is an automatic filter which requires no compressed air or mechanical vibrating mechanism for cleaning the filter bags.
However, the latest product to be brought to the market by SPV is the superheated steam fibre dryer for MDF. If you think this sounds familiar, it is because the development of this innovative system has been going on for some time.
The brainchild of Wolfgang Allerödder, who began development of the dryer as a project for his university degree and is now a senior engineer with SPV, the super-heated steam fibre dryer was developed with some funding towards the total €600,000 (US$606,000) cost coming from the German Fund for the Environment, Deutsche Bundessiftung Umwelt (DBU).
A pilot plant was built at SPV’s Leverkusen works and started trials in the summer of 2001.
The plant consists of a refiner, blowline, gluing equipment and the pilot dryer itself. Resination tests were carried out in cooperation with Dynea.
The dryer operates in a closed-loop system. Wet material is injected via the blow-line and dried in a continuous closed super-heated steam loop, with fibres being discharged via a rotary valve. The recirculated steam is passed through a heat exchanger for super-heating before being re-used for drying.
The advantage claimed for the use of super-heated steam in place of hot air is that the specific heat and heat transfer are higher, while drying takes place in an inert atmosphere because of the closed circuit.
The process steam and the steam evaporated from the fibres can be utilised, for example, for pre-heating the chips, heating air for air grading and conditioning of grader air to control the wet bulb temperature, explains Klaus Radzimanowski of SPV.
The idea for developing the system came from the known fact that drying efficiency increases with a higher percentage of steam in the drying air. Superheated steam is in a condition where it is above the saturation line and is thus ‘dry’, explains Mr Radzimanowski. The more the steam is super-heated, the more its properties approach those of an ideal gas. Theoretically it can evaporate water and absorb steam up to the saturation line.
“The saturation point is constant for a defined pressure which means the saturation point moves up with increasing pressure,says Mr Radzimanowski. “Therefore it is necessary to keep the pressure as low as possible in order to avoid high temperature at the end of the drying process.”
The super-heated steam dryer has an operating pressure of approximately 1.5bar (absolute) and a temperature difference between inlet and outlet of 700C. Outlet temperature will be 10 to 200C above the saturation line.
“The super-heated steam dryer is a flash-tube dryer which means that the drying material [the fibre] is conveyed together with the drying medium while heat transfer takes place simultaneously,explains Mr Radzimanowski.
The steam is transported by a steam fan of special design with a frequency controlled motor. The cyclone is a pressure vessel and thus has to be approved to the appropriate codes.
The fibres are separated from the stream by a specially-designed rotary valve to minimise steam leakage. The steam goes from the dryer cyclone to a collector which defines the pressure in the system. This collector is equipped with a number of steam outlets depending on the number of steam consumers.
The first part is recirculated by the steam fan, the second injected into the pre-steaming bin for the fibre preparation and the third is used to pre-heat air for the graders.
The advantages claimed by SPV for the super-heated steam fibre dryer are firstly that the heat transfer is better. Secondly, the closed loop is completely inert with no, or very low, oxygen content, thus eliminating the risk of fire or explosion. Thirdly, there are no gaseous emissions to the atmosphere. However, because the steam is condensed into water, there is a need for a water treatment plant behind the dryer.
Higher fibre temperature means that the fibre mat has better heat transfer properties although care must be taken to avoid resin pre-cure – hence the involvement of Dynea, which developed a special high-temperature resin.
It is still early days and there have not been any industrial installations of the dryer to date. As it is a pressurised system, and it has to be constructed of stainless steel, there are cost implications compared with conventional blow-line dryers. However, SPV believes the advantages outweigh any disadvantages and several panel manufacturers are reported to be showing serious interest.
Meanwhile the company continues to supply its grading and more conventional drying systems to panel mills around the world.
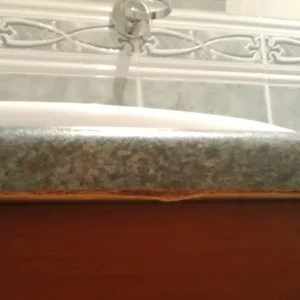