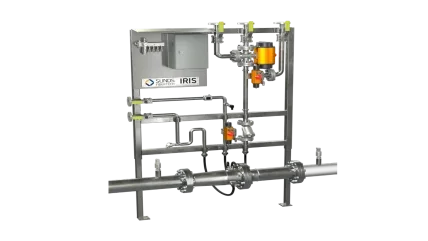
In a video teaser released shortly before the Ligna Exhibition in Hannover, Sunds Fibertech boldly proclaimed it would be launching new innovative products at the exhibition “that no-one in the industry had seen before”.
The fourth generation EVOfuge 360 steam recovery system and a first look at the IRIS (Internal Resin Injection System) gluing technology were the two innovations turning heads on the company’s stand, but there was also breaking news about fresh investment in the Swedish-based business.
A statement was released about investment company Priveq buying a 60% majority stake in Sunds Fibertech.
The move is expected to lead to fresh investment and expansion at Sunds ibertech, which offers products, services and spare parts covering a wide range of wood-based panels production technology.
“Our already strong product portfolio combined with a strong shareholder now creates the conditions for us to become one of the leading companies in the industry,” said Lars Eklund, CEO of Sunds Fibertech.
The company’s plan is to maintain a high organic growth rate, while at the same time enabling strategic acquisitions.
“We are impressed by how Sunds Fibertech has in a short time established itself internationally as a key player in a global market with a few suppliers,” said Karl-Johan Willén, investment manager at Priveq.
“We look forward to, in partnership with founders and employees, supporting the company in its ambitions to put Timra in Sweden on the world map as a centre for fibreboard manufacturing equipment.”
Priveq started in 1983 as part of Skandia and became independent in 1998 under its current name.
Current owners Kenth Eklund and Lars Eklund retain a large part of the company’s ownership and will continue to be key people in the long-term plans the company is making.
GROWTH AND NEW INNOVATIONS
“We have very aggressive growth plans for the future,” Lars Eklund told WBPI at Ligna.
The company’s five-year plan is designed to reach a €100m turnover, one part of which is likely to be strategic acquisitions.
A big emphasis is also being put on product development.
For Sunds Fibertech, the new investment platform represents a fresh chapter in its history. It was formed in 2016, but its background is well documented and can be traced back much further, with expertise relating to the long-standing Küsters and Metso presses.
The company offers new panelboard equipment, including steam recovery, gluing, drying, emission control, sifting and cleaning, forming and mat pre-heating systems, pneumatic systems and automation, as well as refurbishments and rebuilds – such as modernisations for Küsters and Metso Contipress presses. Extensive spare parts is another key feature.
Bernd Bielfeldt, Sunds Fibertech vicepresident of sales for the Europe, Middle East, and Africa region, said the company’s whole team was busy at Ligna, reporting “extremely good meetings and discussions”.
Two big developments on the booth were the fourth generation EVOfuge 360 steam recovery system and a first look at the IRIS gluing technology.
The EVOfuge 360 system is installed between the refiner and resin system in MDF lines to recover steam used in the refining process. The recovered steam replaces fresh steam in the chip bin.
It was first developed in 2011, with the second generation following to facilitate maintenance by adding replacement kit for the wear plate. The third version was to increase steam separation and efficiency. Now we have the new fourth generation “360”.
Visually, the new EVOfuge 360 was a striking sight for Ligna visitors due to its 360O circular design.
Jen Schedin, R&D manager, said the cleanness of steam is further improved with the unique 360O design and the unit also requires minimum installation space.
The circular loop design reduces the pressure drop and improves the separation process even more.
He reported a great response from customers at Ligna to the new design and quoted performance. “We are very proud of this new technology and looking forward to boosting new and existing plants in the future,” he added.
The patented EVOfuge 360 is billed as the only system on the market with no moving parts, using centrifugal force for separation. Basically, the design uses only its shape and steam velocity to generate the centrifugal forces.
The EVOfuge 360’s separation efficiency recovers up to 30% of the steam, while no additional power or auxiliaries are needed, easing its installation and lowering operational costs.
More than 50 units are in operation globally, with Yildiz Entegre currently upgrading its three lines in Kartepe with EVOfuge Generation 3.
Mr Eklund said energy had become a much bigger topic in the last five years with customers demanding energy savings and reduced emissions. Thus, Sunds Fibertech had brought a big focus on developing energy-saving solutions.
The second innovation on display at Ligna was the IRIS internal resin injection system, which enables resin to be injected in the blowline from the middle rather than the outside.
Mr Bielfeldt said conventional resin injection processes could present cleaning difficulties and waste of resin for panel producers.
Finding the “sweet spot” for optimum resin injection and efficiency was very difficult, Mr Bielfeldt added. The IRIS technology features a centrepiece held by three arms, with fibres travelling around the inside of it.
The first industrial trials started on a line in Europe during April and May, with initial results seeing 15% resin savings. Commercial promotion and sales of IRIS could start in September this year.
The company promises further innovations in the pipeline.
SERVICING, MODERNISATIONS AND SPARE PARTS
Even before Ligna, Sunds Fibertech was having a busy time with its growth programmes, such as the launch of its on-stock spare parts programme and the move of its Küsters and Metso Contipress Technology Center to its office in Willich, Germany.
The new location offers sufficient warehouse space for a wide range of standard parts (such as for Küsters and Metso Contipress lines), an enlarged workshop for inspection and repair of parts and office space to host customers.
Beside standard spare parts and the SundsChains, a new Metering spindle exchange programme is available, whereby Sunds Fibertech offers fully refurbished metering spindles with full warranty in exchange for customers’ worn-out spindles. This is designed to save both time and cost for Küsters and Metso Contipress owners.
Mr Bielfeldt believes Sunds Fibertech was unique in its services spanning production, servicing, spare parts and modernisations. The latter areas are helped by its knowledge of the older presses and many experienced service technicians having known the technology for years.
Elsewhere, the company has expanded its representation in Asia Pacific with a new office in Kuala Lumpur in Malaysia, to maximise its support to customers in the region. It is staffed by a local team with long experience in the panelboard market.
Another of Sunds Fibertech’s successful product offerings is its PressBooster mat pre-heating system for capacity increase. The technology was originally launched in 2017 and updated in 2021 with more advanced technology. Today, more than 50 units are now operating around the world.
The Qiannianzhou Group, one of the leading wood manufacturers in China, has four PB/OSB lines – including Rizhao Osborne, Tancheng Osborne and Jiangsu Osborne Line No1 and No2.
It will now install a fourth Pressbooster for its new Line No2 at the Jiangsu Osbourne factory, which produces PB and LSB.
Qiannianzhou Group is the first customer in China with the PressBooster in all its four lines.