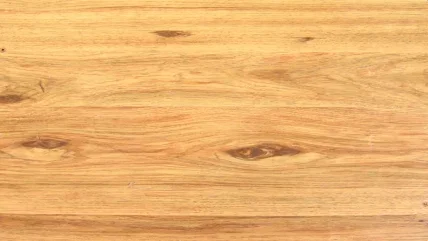
The Berndorf Band Group has been a global leader in the production of steel belts and steel belt systems for more than 90 years now.
The company, established in 1843, is based in the town it is named after – Berndorf in Lower Austria, not far from Vienna. It is a place which is notable in terms of historical industrial development, with the company tracing its history to Krupp, the former huge steel and engineering company.
The company serves various industries ranging from wood-based panels and laminates to the automotive, food, film and foil, and chemical and rubber sectors. The main steel belt production takes places at the headquarters in Berndorf.
With more than 400 employees worldwide and operating in Asia, Europe, and North and South America, the group has eight subsidiaries and many partner companies.
It is the wood and laminate industries that we’re focusing on – these sectors together represent the largest individual turnover segment for the company.
We interviewed Udo Ofenböck, director Global Sales & Service for the woodworking and laminates sectors, who has been with the company 23 years, together with Adrian Miller, director Global Product Management, who joined Berndorf Band Group in 2016 and has a long background in the steel belt industry.
They explained a number of strategic developments and innovations aimed to further strengthen the company and its connection with customers, but first we asked them about how markets had performed during the pandemic.
MARKET DYNAMICS
Looking back, Mr Ofenböck described the situation when the pandemic started in early 2020 – the whole industry was quite anxious and cautious.
“Luckily our industry and our customers in the wood-based panel industry were very successful, because people were investing in their housing, furniture and their flooring.
“2019 had been an excellent year, then 2020 went quite well but was not as successful [due to the start of the pandemic] and we had a slight decrease in our numbers. Business then accelerated in 2021 and was returning to the level before the pandemic started. We have had an extremely good start to 2022.
“Our customers’ plants are very well utlilised and consumers will continue to invest in the products of our customers.”
Mr Ofenböck said another outcome of the pandemic was the working from home trend, an opportunity for customers to sell their products to end users – additional business which hardly existed beforehand.
On the laminates side, Mr Miller identified a trend once the pandemic started of customers taking a break from wanting to develop new textures and designs because they were unsure about the future.
“But laminates were booming and customers could produce in high volumes with their existing textures and having fewer new developments,” he said.
“The continuous production of High- Pressure Laminates (HPL) and MFC is a business where you need high volumes, so we are generally not so affected when new texture development trends slow down.”
This is a reason, he added, why the steel belt business with its high-volume capacity was not as affected as the steel plate sector.
“As a result, the industry could survive these two years without any new big texture developments.”
Mr Ofenböck said Berndorf Band Group was lucky that its staff were not much affected by the virus, so production levels stayed high and the high level of demand could be satisfied with satisfactory lead times. This was boosted by continuously working on production efficiencies and employing and training new staff.
“2022 so far looks like it will be similar to 2021 and we are optimistic that it will be successful,” said Mr Miller.
He predicted that growth beyond 2022 may slow down. “We know the industry will grow but not with the speed we have seen in the pandemic years.
“So far there are no indications that the number of projects will be reduced. There is great potential worldwide.”
Material price inflation has been a reality these past two years for the entire supply chain, whether it is wood fibre, glue or other materials such as the metal alloys that Berndorf Band Group uses for its steel belts.
The company has managed this challenge through a combination of smart stock management and long-term relationships in the supply chain.
DEVELOPMENT AND INNOVATION
Despite the challenges of the pandemic period, it has also been a busy time of strategic planning and developments for Berndorf Band Group.
“We are investing a lot in R&D, service and product management to improve our steel belts for the wood and laminate industries,” said Mr Ofenböck.
The organisation of the company changed at the start of 2022, with two new CEOs being appointed. Additionally, a product management department was established which is independent from sales.
“The goal of the global product management department is to work more closely with our customers and develop individual solutions with them. Especially, in the laminate sector many customers have specific demands related to the steel belt,” added Mr Miller.
This process could then be separated from typical business negotiations with customers.
In the wood-based panel industry, service is at the heart of the customer relationship.
A complete product package is therefore supplemented by training and troubleshooting. Customers are trained to carry out minor repairs themselves so they can continue production until Berndorf Band Group staff arrive to carry out more detailed work.
An important point for a long belt lifetime is preventative maintenance. The Berndorf Band Group service team can help customers receive such trainings for preventative maintenance in order for belts to last longer.
Besides training workshops, the product management and service-teams are executing technical days on customer sites to draw attention to topics like preventative maintenance.
Another development is the mobile belt grinder, a tool that can repair scratches and burrs on steel belts on site to reduce unplanned downtimes. The company is particularly proud of this technology, pointing out that it is the only steel belt supplier to offer such capability. “This is really important in the industry, because capacity is a crucial topic.”
The onset of Covid-19 has also led the company to upgrade its mobile training centre so customers can still receive training despite certain pandemic-related travel restrictions that might prevent them from coming to Austria.
“We have a training centre in Berndorf where customers send their staff and we train them,” said Mr Miller.
“The mobile training centre 2.0 is a good supplement or alternative to our traditional training centre. With the mobile training centre 2.0 we can directly visit our customers on site to train their employees, which is a big advantage in these times.”
Another investment, to serve the laminate industry, is the development of a separate laboratory plate line.
“In order to bring a new texture design to the market we need to have a lab plate as a first step,” explained Mr Miller.
“In the past it took time – three months and longer, which is too long a time to go to market. Now we can deliver lab plates in four to six weeks, and the steel belt within 12-15 weeks, which means we are ahead of the industry in terms of time to market.”
The lab plate line project started in late 2019 but the pandemic delayed it, so it became fully operational at the start of 2022.
Comparing the wood-based panels segment to the laminate industry, Mr Ofenböck said there was a huge installed base in the former, with new projects coming up. Whereas in the laminate industry the installed base of continuous lines did not increase as fast as in the wood-based industry.
Berndorf Band Group has also invested in R&D to work out technologies to create new textures with surface effects.
“In the past the press plate was ahead of the press belt regarding effects – for example in matt gloss effects and also for deeper textures,” added Mr Miller.
“Our product management and R&D departments have developed a new matt gloss technology for continuous steel belts. This technology will help us close the technological gap between press plates and press belts.”
Another highlight is the new production technology of hand-scraped textures. The company has already produced steel belts with a very deep (250micron) rounded texture and also embossed in register for one customer.
The company emphasises that Berndorf Band Group is the only supplier worldwide which offers continuous steel belts for the wood industry and textured belts for the laminate industry.
“This is really unique and we are the only one that can offer that service to our customers,” said Mr Ofenböck.
“Individual R&D projects are undertaken with customers and our experts from the R&D department.”
“We are developing products and processes across the value chain in the R&D department, which is an asset for our future,” added Mr Miller.
Of course, the pandemic has meant many leading exhibitions such as Salone di Mobile in Milan, Ligna, Interzum and others have not taken place. The lack of such platforms is the reason why interior designers, architects and décor producers had less reference for market trends, which may explain partly why the number of new décors has reduced in the prior two years.
Talking to designers on an ongoing basis has therefore become important, including for Berndorf Band Group.
THE FUTURE
We asked the company what the future will look like in five years’ time for markets and the wood/laminates sectors.
“We are expecting a stable growth at least for the next five years,” said Mr Ofenböck.
“There is a considerable number of installed lines, so as long as the consumers are buying furniture and flooring and the construction industry is still growing, we expect a growth in the market for sure.”