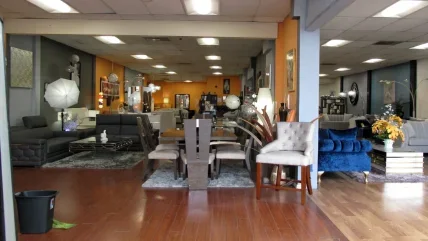
Resin technology is a vitally important part of wood-based panels manufacturing and one company in Greece – NTL Chemical Consulting – has been busy during the pandemic working on R&D and increasing its client base.
The company, founded by managing director Nikos Pargianas in 2008, is located at Thessaloniki Technology Park and equipped with modern laboratory equipment.
NTL says stricter emission requirements and market trends require continuous upgrading and improvement of resin technology and resin plants. NTL provides resin technologies and technical support for customers that want to be at the forefront of these changes.
The company is not a resin manufacturer but provides formaldehyde-based resin technologies, working with an international experienced partner network, as well as co-ordinating with universities and wood technology institutes and working on European funded projects.
The latter included working on a project to develop a special resin to recycle fibres of paper cartons.
Its work also includes training customers’ staff at their R&D and resin plants, application work, troubleshooting and ongoing technical support and a focus on customers’ production quality and capacity efficiency. Complete engineering services for the construction and operation of resins plants are also offered.
Mr Pargianas is no stranger to the world of resins – his experience of around 35 years in the field has allowed him to build an experienced lab team in Thessaloniki, with the company helping clients worldwide.
“We feel very honoured that in these hard times, both old and new clients trust our 35 years of experience and services in order to stay on top of the game and lead in their markets,” he said.
Looking back at 2020 when the pandemic hit, Mr Pargianas said the first half of the year saw the market struggling, but the second half was different, with more activity and better market conditions. Board manufacturers have since registered good financial results against a background of increasing wood and transportation costs.
“There is demand and now some of the customers do not have enough capacity,” he added.
The pandemic has affected travel plans for companies, of course, and NTL has used that one-and-a-half years to rethink and focus on R&D, including look at green resin products and expanding its services.
Specifically, one of the areas of NTL’s research is the development of an adhesive system with a “green” character to be used as a binder for the production of formaldehyde-free (NAF) wood-based panels. This innovative system consists of a bio-resin without the usage of isocyanates with the aim of producing formaldehyde-free wood-based panels.
PROJECTS
As a technology provider and consultant advising companies on the production of resins and their application in wood-based panels, NTL has been working on projects across the world.
“For example, with our associate partners, we have built formaldehyde resin plants in Colombia and resin plants in Korea and Lithuania and now we have demand from India recently as part of a project to build a formaldehyde and resin plant for their new upcoming particleboard plant,” said Mr Pargianas. “We have been asked to provide the engineering to erect a formaldehyde and resin plant there next year.
“Our main job is to provide the resin technology. But sometimes customers want the whole package – including engineering of the plant.”
The project in India is for a 800-1,000m3 a day particleboard operation, with a silver catalyst formaldehyde plant.
“Application experience is very important and is one of our strong points,” said Mr Pargianas. “Most resin suppliers know how to make resins but they don’t always have the application experience. According to the board process production conditions, we know how to make the resin tailored to the precise conditions.
“Another of our strong points is that, due to the fact that we are a relatively small company, we are more flexible, fast and reactive and are able to provide a personal approach and fast solutions to our customers requirements.
“During this pandemic while we are not travelling, we try to keep our customers. We had discussions with a Brazilian company that heard about us and we made an agreement without us needing to travel there. This is a chemical company that has its own formaldehyde reservoir. It is expanding and needs our support for it to compete with the big groups.
“The main task for every board producer is they want to reduce cost and they want to run faster, with lowest resin consumption per cubic metre and low emissions is a main target,” said Mr Pargianas.
One of NTL’s developments is working with a major furniture industry player, within the company’s board production operations. NTL supplies its resin partner a hardener and scavenger as a mixture so they can run a line speed of about 3.6s/m, with emissions of below 2mg per 100g.
“This is a combination of not only the resin itself but also the application process, where attention has to paid to the differences between the core layer, which is very sensitive to humidity and the surface layer.
“We seek to reduce emissions from the core as much as possible – below 2mg for raw board fresh out of the press and less than 1.5mg after seven days’ conditioning. For raw board laminated with melamine paper the emission is actually close to natural wood.”
NTL is continuing research on alternative, green solutions. It has done development work using modified starch featuring no formaldehyde or isocyanates. Lab scale results show cost is higher and line speed slower compared with melamine resins.
“We are following the trend of green resins, as some of our customers are asking for low formaldehyde resins. Because of that we must collect this experience – if the customer wants to make such a trial, we must provide it.”
For some of the customers it is not a main product, but they need to be able to market low formaldehyde products.
NTL has good client relationships in Korea – including providing technology for Foresco to produce its Forescolor coloured MDF boards. NTL works with an associate partner on this project – NTL provides special melamine resin technology and the associate partner supplies the colours.
“Several additives are needed in this process – the challenge is to produce colour continually for more than 48hrs without any stop,” said Mr Pargianas. “If you do not have the correct colours, additives and resin, it can create blockages in the nozzles and production problems.”
Mr Pargianas acknowledges the widespread use of recycled wood in particleboard production, saying the key need is to sort the wood properly before production, while using recycled wood for MDF production was attracting a lot of discussions but short fibres from recycled wood absorb a lot of resin.
When visiting lines in Europe, Mr Pargianas is still surprised to see big resin consumption and slow line speeds at some operations. He emphasised the need to have experienced people who fully understand the entire board production processes in order to operate highly efficient lines, with minimal waste, maximum output and cost-efficiency.
He says he has been impressed with many lines in Asia and South America that have recruited experienced European specialists to help with plant efficiency. He referenced one Thailand plant recording high line speeds and low resin consumption. “Using rubber wood as the raw material, it is a very well controlled process and very cost efficient.
“Everybody talks about low formaldehyde,” he added. “But I am very optimistic that formaldehyde volumes will increase, so that’s why I see new formaldehyde plants. You will still see formaldehyde resins as they are still the most cost-effective.
“We are providing solutions to manufacturers to reduce cost. Faster and cheaper – that is what everybody is looking for – and low emissions.”