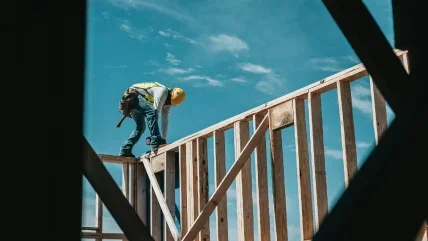
They do things bigger in America. This massive panel is 12ft wide x 48ft long and can come in thicknesses from one inch increasing by one-inch increments up to 24in. Small wonder that they call it the MPP, for Mass Plywood Panel.
Possible uses for it are legion. Its developers say that it is strong enough to form walls, ceiling and structural columns. In off-site construction it may prove a game-changer.
Panels could come from the factory in made to- demand thicknesses and ready-cut to size, with door and window openings already in place. The savings in labour and time at the site would clearly be huge. Recent years have seen the introduction of CLT and of LVL, both of them making slow but steady inroads into the marketplaces. The MPP could prove to be another game-changer in the industry.
Freres Lumber is an Oregon-based company with roots that go back to the 1920s. It is still family owned; no fewer than six family members are actively involved in running it. We spoke to Tyler Freres, vice president of sales, and asked him about the genesis and the properties of these new giant panels.
The potential of panels of such dimensions is obvious. What is less obvious is why it should be a plywood panel. Given the trend toward ever-smaller chips as raw material of wood based panels, would not such a board of OSB or MDF be a more appropriate approach? So why did Freres Lumber choose to use veneers to make their outsize panels rather than doing it from, say, OSB?
“Freres Lumber Co Inc has been for many years one of the largest independent suppliers of engineered veneer for the engineered wood products markets,” says Mr Freres. “So we see wood products through the lens of veneer producers. Veneer is one of the finest products to utilize for next generation engineered wood products because it excels in performance attributes and the veneer manufacturing process allows for very efficient wood recovery from a log.”
The company’s Oregon roots plays its part here. “OSB production has never gained a foothold in the Pacific Northwest. It is primarily sourced from lower-value softwood from Canada and the US South, which do not have the strength properties found in Douglas Fir trees grown here in Oregon. The engineered qualities of Douglas Fir veneer have been well known for decades; in fact it is a large reason many LVL producers are located in the Northwest. Veneer is easy to dry, easy to quantify structurally, and there are abundant quantities available. The company also feels that plywood is a far superior product to OSB, although the cost is higher.”
Were any particular technical problems encountered in sizing-up to this scale, or any radical alterations needed in the manufacturing process, or is it simply made by standard plywood methods done bigger?
“So far, all of our original concepts have proven to be sound,” Mr Freres says. “We produce veneer-based structural composite lumber panels at our plywood facility, join them into a continuous panel, cut to the desired length, stack them with an MF resin, and then press the unit.
"While the original 4 x 8ft panels can be produced effectively, the process of creating a continuous billet with the same structural capacities of solid wood is difficult. As with CLT, removing defects to create a structurally predictable panel has its hurdles.
"Creating a panel with orthogonal layers of LVL would be simpler than our process but it does not lead to consistency and engineering characteristics which would optimise the panel, and you would still be limited to oddply layers for creating structural panels. With our process, dimensional stability is built into every 1in lamella.
"We have chosen a hydraulic press from Minda to achieve panel pressures more appropriate to a typical plywood panel process. We had no intention of using a press that merely made code requirements. Minda was able to achieve the pressure requirements that we requested. The press was designed to our specifications, but is adapted from CLT presses Minda has installed in the past.”
One difference from thinner plywood manufacture is the absence of heat. “Our process developed around the cold press requirements of the MF resin provided by Hexion,” says Mr Freres. “There is no heat added in the pressing process. Due to the natural insulating properties of wood, it would take too long to transmit heat throughout the billet from hot platens. We rely upon the chemistry of the resin and a suitable press time to achieve the required bonding between lamellas.
"Our preliminary design integrates the industry’s predominant thickness of 1/8in Douglas Fir veneer throughout the panel. For a 24in-thick panel there would be 216 veneer plies through the thickness of the panel. We will be developing additional configurations with diverse veneer thicknesses in the future.”
As with all ideas of genius, it seems an obvious thing to do – once someone else has thought of it. What was the spark that set off the thinking behind this? Part of the answer, it seems, was the appearance of cross-laminated timber.
“Freres Lumber has always believed that veneer is the greatest engineered wood product available not only in terms of utility but also in terms of recovery and sustainability," says Mr Freres. “When you are presented with a wonderful product like CLT, it challenges you to produce a product that confirms your belief. Faith is the driving factor.
"We were also forced to think about how to construct and prove the product with our current plywood construction constraints, and these limitations forced us toward the product we have. There are improvements to be made in panel construction to increase productivity. We are aware of these and are working on our next generation of concepts to construct these products.”
And what need is the development intended to meet? Is it a supply-side need – to find a market for veneers – or a demandside need, a gap in the market that can profitably be filled? Is it both?
“Veneer is unique in that, used in combination with modern adhesives, we are able to make products of any size out of small diameter logs that rival the structural properties of any lumber based products.
The fundamental question is whether or not our resin and labour costs offset the potential properties of lumber products. Our raw material, timber, is our single largest cost. To the extent we can use that material more cost effectively the more benefit we gain. We can effectively use a block of timber less than 5in in diameter to create a 4ft wide board with very little waste. The higher log prices get, the more effective we are.”
Pressure from cheap imports was another incentive. “We have also been faced with import pressure for conventional panel products. The US has become the dumping ground for commodity panel products from Canada, Brazil, Chile, Russia, and increasingly China. There are no import restrictions for panel products. There is the Softwood Lumber Agreement which protects lumber based products but that excludes panels products."
Companies need to add value to survive. That was yet one more driver for its development. "We were faced with the issue of finding a value-added product where we don’t have to compete against currency or state-sponsored subsidies that exist for other wood products markets.”
The spark itself was lit on a visit to Austria. “My brother Kyle and I travelled to Europe with a group from Oregon State University. The trip was scheduled around the Ligna show in Frankfurt but also included visits to reputable CLT producers. While we were impressed with the product, we knew that veneer could provide a better solution.
"The layering of veneer in 1/8in layers spreads defects throughout the panel construction for more consistent structural properties without the need that CLT has to eliminate natural defects in lumber by cutting them out and finger-joining the board back together. While wood loss for lumber is based upon grade of lumber purchased, our wood loss is predictable.
"It took several months to return and develop potential layups and to determine testable resin formulations. With the help of Georgia Pacific and Hexion we were able to develop potential proof-of-concept layups. When the initial testing proved favourable we filed for patent in October 2015.”
Thereafter things moved quickly. “Thanks to our tight family corporate structure, and the support of all our shareholders, we were able to approve the initial test facility within eight months of proof of concept. The Purchase Orders for the entire facility were initiated within a year of patent application
"We broke ground for the 4-acre production facility in March 2017 and have proven first construction through the facility by December 2017. It has truly been an expedited schedule that we don’t think could have been achieved without the full support of all of our family and the hard work and dedication of key employees. We are also blessed to be in an area where there are extremely competent and trustworthy contractors and suppliers who exceeded expectations.”
The MPP is said to be the largest panel in the world. The size of 12 x 48ft came about almost automatically.
“Veneer is typically produced in a dry format of 49.75 x 101.5in, and finished plywood panels are 4ft wide x 8ft long. Widths of 8, 10 and 12ft are easy to achieve with standard plywood,” says Mr Freres.
“The 50ft press length allows us to produce a final product over 48ft long which is a typical length for most LVL products and is a length that is easily transported to the job site. We will be certified for Structural Composite Lumber under product code ASTM D5456. We have built in the capability to produce up to a 60ft continuous panel at a later date if we would like to increase the capacity of our processes.”
On performance, the parameters so far tested have been found acceptable, and as good as CLT or better. “On equivalent volume basis, ie, equivalent thicknesses, we are stiffer than the PRG-320 CLT standard in the major force direction. Additional testing is needed to prove performance in the minor force direction. We believe we will surpass structural properties in both directions.
"Our panels are significantly denser than lumber-based panels due to the densification that occurs in each step of our process. Panel weight is around 37 pounds/ft3 as against typical weight of 33 pounds/ft3 for Douglas Fir. As such, in areas where density improves performance we will out-perform. It is also fair to say that in areas where panel density is a detriment, we will under-perform. Acoustic properties have not yet been tested.”
“Oregon State University, and later the TallWood Design Institute (which is a partnership between Oregon State University and the University of Oregon), provided technical expertise in testing and in potential market development.
"Their expertise and relationship has been invaluable and we will continue to work with them in the future. Hexion has also been essential to our product development by providing the technical expertise and advice on production processes.
"We were fortunate that their development of a honeymoon-style resin coincided with our product development and we were able to integrate their process directly into ours. We believe that our partnership with Hexion has established a superior bond between panel lamellas that will improve panel fire resistance.”
Patents for the process are currently pending. The initial investment in the production facility is expected to exceed US$30m, with further expenses going forward to optimise existing production processes to the new product. So much for the product itself. What of the users of it, and when can they expect it to be available? “We have had interest from all sectors of construction” says Mr Freres.
“Multi-storey, multi-family, single-family residential, non-structural applications and so on. However, until we achieve product certification we cannot provide a product report for structural applications.
"We will not produce structural panels for the market until we are certain of the quality, consistency, and performance of our products, and APA certification is essential to that process.”
A major application could be in off-site modular construction of homes and other buildings. “We believe that we are uniquely situated to provide solutions for the prefab or modular residential market. We can produce a large-format 12ft wide x 48.5ft long panel from minimum thicknesses of 1in to maximum thickness of 24in.
"We can CNC the panels to the dimensions required for a specific construction. While full size panels exceed what people can lift we can make them into increments that can be handled by two people. We welcome any requests for panel dimensions. While construction processes have traditionally relied on a significant amount of manual labor, mass timber construction lends itself to construction with heavy equipment.
"Modern construction requires modern tools, and more efficient use of labour. As experienced labour becomes more difficult to employ we see pre-fab construction as a way to mitigate costs. We hope to pre-install all connection systems for future panels, allowing for rapid on-site construction.”
Its cost-saving advantages – of speed of construction, and avoiding the shortage of skilled labour – are even more valid in the US than in Europe. “The main problem to be overcome is persuading users of its reliability. The primary hurdle is determining the metrics which would convince the construction industry that not only are mass timber panels the most cost-effective approach to construction, it is also the most risk-free.
"If an architect gives us the specifications we can cut the panels to the sizes and shapes that he or she needs. Right now, we believe we can be flexible in supplying smallvolume shapes and sizes as long as we are provided with a design or CAD file that can be translated into production – though the consumer does need to be certain regarding design before the manufacturing begins. We cannot un-cut panels.” That said, there is clearly potential here.
But massive plywood panels are not intended solely as a solution for replicable modular replicable construction.
“We see it also as ideal for mid-rise projects. There we hope to start small and grow bigger. Our goal is to be ready for potential International Building Code changes which may allow mass timber construction up to 18 stories by 2021.”
It may not be coincidence that the Framework Building, at 12 storeys and 148ft, now being erected and one of the tallest wooden buildings in the US is in Portland, Oregon, and that Tallwood was involved in testing the design.
As a material MPP should be costeffective, with advantages over CLT. This is partly achieved by the fact that the panel can be produced in the exact thickness that is structurally required.
“Cost-effectiveness is achieved by tailoring a panel more closely to the thicknesses required for the structural properties of the project. We should not have an odd-ply requirement due to cross-banding built into each individual lamella. As such, our eightinch panel will perform to the approximate characteristics of nine-and-three-quarter inch CLT, leading to a 20% saving in wood.”
And ply gives the advantage of quality consistency without waste of raw material. “There are knots and defects in our panels, as with any naturally occurring product. The difference is that all defects are limited to the thickness of the veneers peeled and then latticed with veneers in additional layers. The net effect is a predictable product with minimal structural defect.
"We density grade every veneer that passes through our facility so we know the performance characteristics of each veneer.
As such we can change the density grade, the visual grade, or the orientation of every veneer to meet the structural requirements of any project. While we will be limited by certification requirements initially, we anticipate varied performance qualities for appearance and structural properties going forward.
"In addition, the recovery of fibre going to higher value products is higher for veneer operations than for lumber operations. There is also a vibrant market place for all engineered veneers in the Pacific Northwest which makes efficient use of high-density graded veneer. The mass of our panels indicate that we can put lower density grades of veneer, which are abundant in the current market, to better use.”
It is eco-friendly in other regards also: “Our average log diameter through our primary engineered wood products veneer plant is about 8.5in. As such, we are uniquely able to utilise smaller diameter logs for the production of advanced wood products. The smallest diameter we peel is only 4.75in. We will gladly utilise any thinning, second or third growth fibre available.
“We believe our products will be longlasting. We hope that North American consumers will adopt an ethos that our structures are built to last. The interior of structures can change but it is difficult to change the bones. We need buildings that can withstand any calamity, not ones with a short life-span that survive some. With appropriate care, there are wood structures that have lasted for a thousand years.
"We believe that Mass Timber Construction is the way of the future. We intend to be a product that provides the evolutionary leap in performance.”