Villa Cortese, near Milan, has been home to Imeas Spa since it was founded over 40 years ago to build grinding and sanding machines for the stainless steel and wood based panel industries and it remains the world’s foremost producer of grinding machines used in the production of endless stainless steel belts for continuous presses.Over the years, the company has added other substrates to its portfolio, including plastics and composite materials, but the wood based panel sector remains its most important market. This variety of materials to be surface-finished has presented Imeas with a number of different challenges requiring different techniques, but it has also enabled the company to transfer the knowledge gained in one area to its other areas of activity. The panel industry has also changed dramatically in the past 42 years – and continues to make new demands on its sanders. Raw materials used in particleboard and MDF have changed and each wood type has its own peculiarities with regard to successful surface finishing.
However, perhaps the most consistently increasing demand has come from the ever-rising production speed of continuous panel production lines. No panel mill can afford to have bottle-necks in a fast-moving production process and the sanding line is a classic example of where such delays could occur. Increasing the feed-speed of a sanding line may seem a fairly simple matter to achieve. However, maintaining a high-quality finish at the same time is the challenge as contact time between panel and abrasive belt is reduced, as Francesco Zenere, son of the company’s president, and its sales director, explains. We have made improvements to the machines we offer to these high-speed lines and we are now able to offer a solution to our customers,he says.
“From our experience in stainless steel polishing we know the trade-off there can be between line speed and product quality. You can increase the number of sanding heads but this is an expensive option and is not always practicable for reasons of space and so on.
“The alternative which we offer is that the last two or four sanding heads can be individually adjusted for speed. Thus in the ‘classic’ sander, with two calibrating and two finishing heads, at least two of these heads would have adjustable speed. All heads can be included, but the minimum we advise is two heads.The principle is to adjust both the feeding speed of the line and the speed of these final heads in the concept marketed by Imeas as Variable Belt Speed, or VBS. We offer this system on existing as well as new machines as it does not involve a mechanical alteration but only an electronic one,continues Mr Zenere. The system is based on inverter technology, with a variable frequency drive controlled by the PLC – the system can in fact be switched on and off by the operator if required. The feed speed of the line can also be linked automatically to the speed of the final two or four heads and they are always linked in a constant ratio, where the faster the feed speed, the faster the belt speed.
The Cross-Transversal Belt Sander, CR-TB, was developed five years ago by Imeas to give a super-fine finish, but was intended for lower-speed applications. The VBS, on the other hand, can run at © p44 ß p42 speeds of up to 150m/minute and has already run at 120m/minute. The first VBS was offered to the market in March this year and one upgrade has already been ordered, with several more under discussion, says Mr Zenere.
“We can offer VBS in a package with the CR-TB if required – the transverse sanding gives a different kind of finish to the normal uni-directional process. It also offers a 15-20% saving in paint/lacquer coatings; or better application of melamine papers due to increased contact area. You can also use thinner papers.”
Imeas has kept to its traditional steel frame construction for its wide-belt sanders, using thermally-treated steel to provide a stable construction with even expansion and contraction throughout the machine. “Steel construction is also easily customized for customer requirements. For instance, sanding cork material which is tricky because it is brittle,explains Mr Zenere. Imeas also offers its ‘eXtended technology’, which offers extended abrasive belts of 4m in length, giving a 25-30% longer life. Sonae Indùstria’s White River factory in South Africa has recently bought a calibrating and sanding line comprising two machines with a total of eight heads and a maximum working width of 2.9m. The first four calibrating heads have 500mm steel rolls, followed by four finishing shoe units.
In 2001, Imeas saw the opportunities presented by the Chinese market and set up a joint venture in Suzhou – Imeas Sander Manufacturing Co Ltd – to make only four feet wide machines with four to 10 heads. The wide-belt machines are still solely manufactured in Villa Cortese. That things are going well for the Chinese subsidiary is evidenced by the fact that it is about to undergo relocation. In fact, the factory had to move from its first address due to the government designating the locality as a tourist area. However, that second factory is now too small and the company will be moving to larger premises in the same city by the end of this year. Imeas Suzhou sells most of its production on the Chinese domestic market, but is also licensed to sell into Pakistan and has received orders from there. It is also licensed for export to North Korea, Vietnam and Cambodia, while India is showing promise as a potential market. The Chinese company does offer spare parts, service and support for the machines imported from the Italian factory and has IT technicians who can handle installation and set-up.
Imeas also has a wholly-owned subsidiary office in Beijing for sales and field service.
For the North American market there is Imeas Inc in Peach Tree City, Atlanta, Georgia, with Nathan Rutherford as president. It offers sales and service to all Imeas’ markets in all customer industries in North America. Imeas Australia is another sales subsidiary, located in Melbourne, and the company has sales agents in many countries throughout Europe and North and South America. At the Xylexpo exhibition in Milan in May, Imeas finalised a deal with a major panel manufacturer in Brazil in which it will supply four sanding platen units to go after an existing machine to improve the panel quality. Orders taken in 2008 include three machines to Russia (Tom Lesdrev, PT Rihau and Abinsk), a new sanding line for Interbon in Spain, two lines to Yingang in Hubei, China, a line to Chilean-headquartered Masisa for Brazil and an addition to an existing machine at Yildiz Sunta, Turkey. Turnover for the whole Imeas company exceeds e20m. Other orders will take the factory in Villa Cortese into 2009, which, in common with other machinery makers across the industry, looks like being another good year.
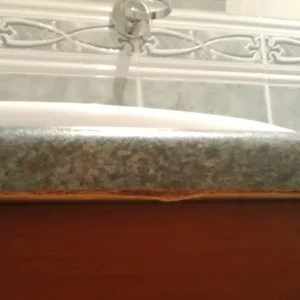