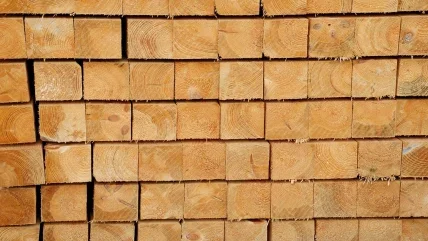
When news came some months later that the owners would rebuild after the fire damage, the response was amazing. While the decision was taken not to reinstall the peeling lines, the owners instead opting to source green veneer from nearby mills, a plan was implemented to salvage as much of the drying and lay-up as possible to make reopening the mill financially viable.
Needless to say, the news that Boise Cascade would reopen the mill was met with enthusiasm, particularly after it was announced that workers idled by the fire would participate in the equipment salvaging efforts – a key component in getting the mill back up and running. To the mill owners it made good sense to employ their own people in the rebuilding efforts, since they knew best what could be done with what remained of the mill’s salvageable machinery and equipment.
Boise Cascade’s involving its employees in the rebuilding effort was laudable, but what was truly amazing was the speed with which the mill was back online. Barely a year after the fire, plywood was again being produced at the Medford mill and close to half the mill’s employees were back working. Today, staffing stands at 350.
Perhaps that’s why the Medford mill is considered a model of what can be achieved when the corporate world and the community in which it operates unite to achieve common ends, and why Boise Cascade and then area manager, Dick Rudisile, now five years retired, received Community Spirit Awards from the Medford/Jackson County Chamber of Commerce. Oh, and it should be mentioned that the salvage efforts halved the cost of rebuilding!
Drying – A critical component
David Elliott, region engineer at the Medford mill, had taken up his new position shortly before fire ravaged the mill.
“My responsibilities during rebuilding efforts in 1999 were carried out in my role as assistant region engineer. At the time I was responsible for handling most other engineering projects on the company’s behalf in the region. Like my predecessor, Bob Morris, I was but one resource among many. A lot of people put a lot of effort into getting the Medford mill back on its feet,said Mr Elliott.
He explained that the mill’s six longitudinal dryers, although damaged by fire, were all fully operational again by April 2000, at which point drying capacity of the Medford mill stood at 370MMSF (3⁄8in basis), or 330,000m3, annually.
Mr Elliott stated further that drying veneer is a critical component of Boise Cascade’s regional ‘enterprise model’, which encompasses several green veneer mills, an engineered wood facility and the Medford and Rogue Valley mills.
Green veneer is brought to Medford from nearby White City, where Boise operates two 8ft and one 4ft lathe, and Willamina, where they have one of each size. Veneer dried at Medford supplies lay-up lines at Boise Cascade’s Rogue Valley mill and at the Medford mill. All told, annual drying capacity at Medford is around 600MMSF (3⁄8in basis), or 530,000m3, with potential for increased output.
“The market has been down in recent years, but we haven’t been idle at Medford,said Mr Elliott. “In 2009 we installed the first of two jet dryers, which increased our dry veneer production, eliminated a high-maintenance and inefficient dryer and improved air quality inside and outside the mill.”
Mr Elliott said that replacing the 50-year-old longitudinal dryer with the Coe jet dryer in 2009 required buy-in from the operators who were, understandably, uncertain as to the virtues of jet drying technology, but who soon embraced it once they saw what the Coe dryer could achieve.
“It’s our muscle dryer,said Mr Elliott, referring to the high volume of dry veneer the Coe system puts out.
Soon after installation of the Coe dryer, discussion turned to further upgrading of the mill’s drying capabilities and in early 2010 management decided to purchase a second jet dryer, this time from Raute Canada. David Elliott explained why: “With our existing longitudinal dryers and the recentlyinstalled Coe, we had the capability to dry plenty of wood. What we saw in the Raute system was the ability to add finesse drying to our mix. By that I mean a dryer that would provide good drying capacity but which would also improve the quality or our higher grades by reducing case hardening, over-drying and breakage”.
The Raute jet dryer, according to Mr Elliott, monitors and adjusts humidity in the dryer to improve veneer quality. It does so by using a computer to open and close dampers in the dryer’s three temperature zones.
“The dryer’s speed control is affected, in large part, by the moisture content of the veneer. The common perception is that drying veneer in a humidity-controlled environment improves veneer quality,he said, adding, “We’re still climbing the learning curve as far as setting dryer recipes and operator training are concerned. But, we’re confident we’ll achieve the results expected with the supplier’s continued assistance and the expertise of our operators.”
Additional work in-house
To accommodate the heating requirements of the new dryer, the mill replaced the existing 8in steam line with a 12in line, effectively decreasing pressure losses and increasing transmission capacity.
The mill’s own personnel also took two existing 10-bin dry stackers and rebuilt them into one 12-bin unit, which they installed behind the new Raute dryer, and an eight-bin stacker, which was incorporated into a stand-alone re-feed line.
With installation of the latest dryer now complete, the mill has six dryers in total – four of the original longitudinals salvaged from the fire of 1998 – and two six-deck jet dryers installed within the past three years.
All these dryers are equipped with Ventek moisture meters and camera graders.
Clearing the air
Perhaps the most outstanding feature of the Medford plywood mill is not so much what the mill has, but what it lacks; something that is highly conspicuous by its absence; a requirement mandated by Boise Cascade management and one that David Elliott and his colleagues strive constantly to achieve.
What Boise Cascade’s Medford plywood mill lacks is an atmosphere, both internal and external, contaminated with airborne pollutants – one that comes as close to achieving zero emissions as is, perhaps, possible.
According to David Elliott, they have achieved this enviable goal largely by adhering to the very strict guidelines laid down by environmental entities, like the Oregon Department of Environmental Quality, and OSHA, the government agency responsible for workplace safety.
“Adhering to the requirements of these outside agencies has figured strongly in Boise Cascade’s compliance with environmental programmes, certainly. However, I would also say that the success we have achieved here at Medford, as far as environmental stewardship is concerned, has just as much to do with Boise Cascade’s own self-generated safety and environmental standards regarding the operating of a clean plant.
“Our own commitment is just as important, if not more so, than that of our governing agencies,stated Mr Elliott.
Taking in the atmosphere inside the Medford mill, one would have to agree that the management of the Medford mill have achieved their goal: It’s like a breath of fresh air.