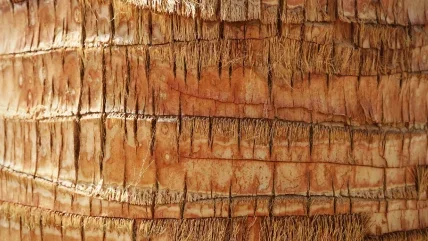
When we think of palm trees, several images come to mind – idyllic scenery on a tropical island or maybe much-maligned plantations in southeast Asia for harvesting palm oil.
But we might not realise that palm could potentially be a major source of wood in the years to come, with the waste trunks being turned into value-added wood products. With pressure on timber resources globally, and increasing competition for wood fibre, new sources of usable raw material could prove very important in the future.
A number of machinery and equipment companies serving the woodworking industries have thrown their support behind the PalmwoodNet project, funded by the German government, to tap this hitherto largely underutilised resource.
The project, sponsored by DEG (Deutsche Investitions und Entwicklungsgesellschaft GmbH) officially began in November 2015 under the leadership of the project co-ordinator, adhesives manufacturer Jowat SE.
Research results were shared at the recent Ligna exhibition in Hannover; and they are encouraging.
Project Background
So why oil palm?
The resource is large and getting larger – the total plantation area for oil palms amounts to almost 50 million acres worldwide.
The palm oil itself is used in the food and biochemical industries as well as for energy, but the oil yield decreases significantly after a palm tree reaches the age of 15-20 years.
For this reason, plantations are cleared and replanted after 25 years. Based on a planted area of about 50 million acres, an average of almost two million acres would have to be replanted annually on a long-term basis.
As a result, large volumes of oil palm wood accrue during replanting of 'unproductive' plantations in Asia, Africa and South America, with estimates forecasting 100-120 million m3 of trunks per year. The leading oil palm producers are Indonesia, Malaysia, Thailand and Nigeria.
The trunks are commonly left to rot, chipped as fertilizer, or even burned. The main reasons for not using the wood are the extreme density distribution within the trunk, the very high moisture content, and the significant difference in structure and properties of oil palm wood in comparison to 'normal' wood species.
Earlier studies and pilot projects on the utilisation of oil palm trunks for products have shown high technical and economic potential but there are no industrial implementations yet for the reasons outlined above.
Until now no comprehensive solutions, and very little information on products, markets and processes, have been available to investors and companies who are interested in utilising oil palm wood. Additionally, machines and tools have to be adapted or optimised for processing oil palm wood, which has some unique challenges.
Wood Characteristics
The wood’s density, and its physical technological characteristics, vary significantly across the trunk. Density varies from 150kg/m3 to 700kg/m3, with the outer trunk timber being the densest and inner wood being the least dense.
Hard and long woody dark fibres – which when viewed in a cross-section have the appearance of 'PAC-MAN' (the character in a 1980s amusement arcade game) can be detected in the wood.
These give the wood its strength and are embedded in a very soft cell matrix. It is this unique structure that means special process technologies and recycling strategies are necessary, depending on the different density groups. The fibres must be cut exactly, without crushing down or ripping the cells during processing.
Tests have shown that an extremely large shear angle and specific tooth geometry are required for effective cutting without damaging the wood.
The wood’s tensile, pressure and bending characteristics are described as good, but due to the structure, the characteristics across the fibre, and the behaviour under shear stress are reduced.
Benefits include a uniform quality timber due to lack of knots and growth-related defects, while the unique wood grain structure enhances the aesthetic value of the product.
Oil palm trunks have a very high moisture content (150-600% based on the dry mass). Due to this moisture content, and the sugar and starch in the wood, fungal decay starts very quickly. Preventing the decay requires special logistics in the supply chain from the logging of the palms to processing; and a very complex drying process.
Some of these drawbacks – and the fact that raw material alternatives are still available from natural forests and that the decision-makers still focus mainly on the oil palm fruits – have been holding back the industrial development of oil palm wood.
Product Development
To support the project, different companies and institutions have joined PalmwoodNet in a multi-stakeholder approach.
The five core partners of are Jowat SE, Minda Industrieanlagen GmbH, Möhringer Anlagenbau GmbH, Leitz GmbH, Boehlerit GmbH and Palmwood R+D in Freiburg, as well as various German universities and other industry partners who will assume specific development and implementation tasks.
A number of other project partners, including R+D institutions, universities, woodworking companies and plantation holders from Malaysia and Thailand, have been integrated into the network.
Only plantation holders who have certified a substantial share of their plantation area according to international standards can participate in the project.
The first phase of product development has looked at producing dried lumber in standard sizes; finger-jointed and moulded products; glued products; cross-laminated lumber; one layer edge-glued panels; panel cores; composite panels; laminated flooring; and lightweight furniture elements.
The Forest Research Institute Malaysia, Malaysian Timber Industry Board and the kiln dryer manufacturer Visdamax have been involved in the first industrial trials to produce kiln dried oil palm lumber.
At the recent Ligna exhibition in Hannover, tooling producer Leitz said its role was focusing on processes to optimise manufacture of the product.
Both Leitz and Boehlerit are looking at cutting processes and outlining suitable working steps and procedures. More specifically, this entails the development of suitable cutting materials and tools for achieving the required quality and efficiency of cutting processes.
“The problem is that this wood has a lot of abrasives in it,” the company said. Production systems have been installed to generate different surfaces.
Leitz’s CEO, Jürgen Koppel, said one solution for using the material as furniture where components need to be inserted was to use different densities of the wood in certain areas, removing the need for special nails.
Samples of panels and door elements, made in cooperation with Meisterschule (School of Apprentices) in Ebern in Germany have been made using 100% oil palm wood, or just the core in palm, with the face layer composed of other types of veneers.
Sample doors have been produced which are 3kg lighter than a conventional wooden door, while the same sound insulation performance as particleboard is possible.
This lightweight feature sees palm wood as ideally suited for use as a light core layer of a panel finished with surface layers of other types of wood material.
The Way Ahead
Ideally, PalmwoodNet’s target is to see a sawmill built in a region where there are large volumes of oil palms. Its research work, which runs until 2018, includes analysing and assessing the ecological, economic and social effects of utilising oil palm wood. Continued analysis on product types and designs will also feature, as will developing marketable products for existing or expected demand.
Further research work will be conducted on developing machines, tools and cutting materials and optimising manufacturing processes. Models showing the manufacturing cost, return on investment, payback period and risks are also being drawn up, along with determining an accredited certification system for proving sustainability.
There will be active co-operation with Asian partners from the R&D sector, processing industry, associations, plantation business and NGOs. Document properties and manufacturing processes will be compiled in a manual and website for knowledge transfer.
Of course, success of the project will ultimately depend on whether investors get behind it so that an industrial production facility can be established. It may be a while yet before palm wood panels and lumber become the material of the future and are on volume sale in the UK and Europe, but it is encouraging to see that untapped wood raw material streams are ready and available for the years ahead.