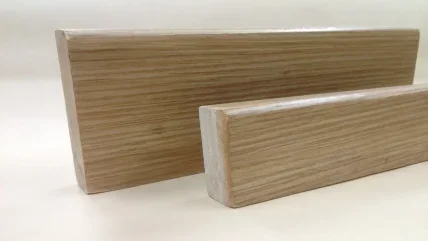
2017 was a record year for plywood, with 161 million m3 produced worldwide. The FAO (UN Food and Agriculture Organisation) recently identified 109 countries which manufacture plywood, ranging from Cyprus with only seven m3, to China with 117 million m3. The upward production trend in China is unprecedented.
North American production roughly stabilised at 0.85 million m3 of hardwood, and 12.45 million m3 of softwood, plywood.
How has the North American industry recovered from the brutal economic conditions of the Great Recession (2008-9)? Is the North American plywood industry still viable after the attrition prompted by a growing acceptance of lower-cost competitive products, such as OSB? How many plywood plants will continue to operate? How much panel demand will be replaced by substitutes like OSB, MDF and particleboard? What will be the short-term and longer-term effects of tariffs first imposed on hardwood plywood, and later on certain softwood plywood, made in China and exported to the US?
Coming of age
The industrial manufacture of plywood, descended from veneer-based processes of ancient China, Egypt and Greece, was introduced at the 1905 World’s Fair in Portland, Oregon (US). In the following century, the industry has enjoyed eras of robust sales and also suffered through periodic downturns.
The plywood industry’s historic response to adverse conditions has been to invent new products, find new applications and manufacture more efficiently.
Observers have remarked that plywood has at least 10,000 uses and new applications are continually discovered.
Veneer-based products, which feature cross-banding of odd-numbered layers of veneer, can be manufactured with a wide range of tree species and technologies. This versatility makes plywood an ideal product for applications ranging from basic sheathing and industrial components, to highly-engineered structural designs.
Table 1 illustrates global production and percent production by region during each of six decades (1967 to 2017) and for all types and grades of plywood (both softwood and hardwood). The table highlights the development of plywood as a global industry, as well as relative regional growth.
In recent decades, the North American experience has markedly differed from the rest of the world. Northern America's production (defined as Panama and north, including the Caribbean, even though Canada and the US comprise more than 99%) peaked at 23.6 million m3 during 1987 and then trended downward concurrently with increased acceptance of lower-cost OSB. Northern America made over half (56.3%) of global output in 1967, but declined to 7.6% by 2017.
However, remarkable growth in South America, Europe and China has more than offset the decline of North America.
Production by Region
The Great Recession exacerbated the plywood industry’s decline in North America. In contrast, plywood production has exponentially grown in Asia, particularly in China. (see Table 1).
Asian production slowly but surely grew until the early 1990’s, when continental production mushroomed as the Chinese industry developed. China currently has thousands of plywood plants (possibly as many as 5,000), with a range of technologies from primitive to modern.
Table 2 identifies the current global production share; China manufactured 73.1% during 2017, with the rest of Asia producing 15.4 million m3, for a total Asian share of 82.7%. North America produced 6.0%; a few European and South American countries collectively manufactured much of the balance.
The North American industry was ‘rightsized’ during the Great Recession. Georgia Pacific permanently closed thirteen of the 22 factories it operated in southeastern US. Other manufacturers, in both the southeast and western North America (principally British Columbia, Oregon, and Washington), also closed operations around that time. North American softwood and hardwood plywood mills' annual production capacity is now about 17,000 million m3, with softwood production at around 80% of cumulative rated capacity and hardwood at about 50%.
North American Construction
In North America, almost all plywood is directly used in construction, or in a product (such as furniture and cabinetry) that a consumer would purchase for a new dwelling. US housing starts of about 1.25 million per year in 2017 remained well below the 1.6 million average prior to the 2008 recession. Now that rising interest rates are increasing monthly mortgage payments for a typical consumer, it's unlikely that housing starts will soon return to the pre-recession level.
Increased us plywood imports
Post-Recession North American plywood mill capacity roughly matched supply with expected domestic and net export consumption. However, beginning in 2016, the strengthening US dollar and relatively strong US economy began drawing offshore plywood to the United States; 2018 was expected to be a record year for plywood imports.
Softwood plywood imported into North America (mainly the US), principally from Brazil and Chile, is typically made from Radiata (P radiata), Caribbean (P caribaea), Slash (P elliotti) and other pine species. South American pine plywood certified to meet US building code requirements is readily accepted as a building material. Imports continue to pressure North American manufacturers by limiting prices.
In 2017, the US International Trade Commission (USITC) imposed punitive antidumping and countervailing duty tariffs on hardwood plywood imported from the People’s Republic of China, which is often used in furniture and cabinetry. US hardwood plywood makers complained that PRC plywood producers enjoy unfair cost advantages.
Monthly hardwood plywood imports from China fell by more than half in 2017. However, plywood imports at the end of 2018 are higher than at the end of 2016 as importers have purchased hardwood plywood elsewhere (such as from Cambodia, Russia and Vietnam). Chinese producers purportedly evaded tariffs by shipping re-labeled product through third party countries and Chinese producers modified hardwood plywood recipes to meet the harmonised customs definition of softwood plywood.
Recently, USITC ruled that the tariffs will include softwood plywood types which principally originate in China. On balance, tariffs have not brought substantial relief to US hardwood plywood producers.
Crossing Boundaries
Apart from economics, other factors are important in import and export decisions. Non-monetary factors include compatible product specifications and standards; the need for non-local products; and shared energy/environmental expectations.
The import or export decision is not always related to cost or availability. Increasingly, the search for a cheaper, functionally better, or more attractive, plywood panel has gone international. The user becomes willing to pay a premium if the imported plywood is perceived as a superior product when compared to current sources.
However, a typical question frequently asked prior to a purchasing decision is: “Will this product be available longer-term and will it consistently perform as expected?” The following describes a case in point:
The supply of Doulas fir face grade veneer, originating in western Canada and the western US, has declined as the scarcity of old growth Douglas fir (Pseudotsuga menziesii) requires a transition to second growth Douglas fir.
The second growth product requires more face repairs, but this repair step is costly and often fails to achieve an aesthetically pleasing result. Users in the US discovered that Chilean A-grade Radiata pine, requiring relatively few patches, is often a better solution. The visual preference is reinforced by the strong US dollar.
Product and performance standards are crossing boundaries. For example, US Department of Commerce PS-1 Performance Standards are followed by Brazilian plywood factories which ship plywood to the US. North American plywood producers will typically manufacture and certify plywood to four or more national standards. The same trend is occurring with European makers, but exporting is made easier with EN 13986, the ‘harmonised’ European standard for wood based panels.
Increasingly, market demand is being met by global producers who are capable and certified to manufacture plywood to a host of standards. The comparative strength of local and export markets, currency exchange rates and tariffs, also heavily influence the import/export decision.
Manufacturing Technology
A southern European equipment supplier recently installed a veneer dryer in a southeastern US plywood plant. In, turn, an American firm sold several veneer dryers in Russia. These examples highlight emerging trade practices: Plywood and veneer equipment suppliers now regularly cross boundaries to seek new customers.
Two recent North American trade shows are reminders of the increasing internationalisation of the industry: The International Woodworking Fair (IWF), held in Atlanta in August 2018; and the Timber Processing & Energy Expo (TP&EE) at Portland, Oregon (US) during October 2018. Such trade shows facilitate efforts to establish cross-border connections between suppliers and users of wood product manufacturing equipment.
Energy and the Environment
Energy consumption and environmental awareness are becoming integrated issues which influence purchasing decisions across national boundaries. Various energy and environmental standards, such as LEED (Leadership in Energy and Environmental Design) as a globally recognised symbol of building sustainability, are becoming increasingly important sales tools.
Another example is the Forest Stewardship Council (FSC), which certifies that wood products originate from forests managed in accordance with environmentally, socially and economically responsible practices. FSC and similar standards are becoming increasingly influential to plywood producers seeking to serve domestic and offshore customers.
Continuing Transformation
Growth in Asian production and consumption can’t continue at the present pace, given the decelerating growth rate of the Chinese economy and constrained wood fibre supply. North American supply roughly matches demand. However, changes are inevitable in both cases. What, then, is the future of the industry within these two regions and the rest of the world and what will be the tenor of future updates?
The consumer continues to consider plywood an unique product because its strength and appearance attributes are not easily duplicated. Balancing supply and consumption in North America, and continuing to grow volume elsewhere, will hinge on a number of factors. General economic conditions, including the relative strength of the US dollar, will remain major factors.
A developing model to grow the North American industry embraces basic plywood technology, but broadens use of the key veneer and adhesive components. The plywood which has existed for more than 100 years continues to be a major product and, simultaneously, there is a new generation of veneer-based technologies. Laminated Veneer Lumber (LVL) is one such product, built to achieve certain strength and other values. Similar to the ongoing process of OSB supplanting plywood sheathing, LVL commonly replaces timber, steel and concrete structural beams in construction. The product has gained broad acceptance in North America and is now positioned to be accepted in the rest of the world.
Plywood technology is spurring the development of additional veneer-based panel products. Freres Lumber Company, a sizeable veneer producer in rural Western Oregon, is providing the latest example.
A cooperative research effort between Oregon State University and Freres Lumber Company invented the mass plywood panel (MPP). This engineered panel is intended to substitute for lumber, steel and concrete better than Cross-Laminated Timber (CLT) as a structural element in construction.
The invention of MPP is the latest indicator that veneer-based technology is conceptually sound and that veneer can be used to manufacture an ever-wider array of useful products.