Another Egger plant at Suceava in Romania has a replica of that Hexham line. In South Korea, Texpan is updating existing forming machines at Dong Wha. In Indonesia, PT Kutai Timber, which is owned by the Sumitomo group, took delivery of a three-head stationary forming station and a hammer mill for chip preparation in July this year. Fantoni’s Lesonit MDF mill in Slovenia received its forming machine and storage bin for MDF in June, while Masisa of Chile’s machine for MDF started up in July. Two contracts in Iran for MDF mills and three OSB forming machines for North America all demonstrate the worldwide, and industry, coverage, says Mr Zoppetti. Latest products include a new automation system between the weighing and the regulation of the forming machine, with a special system to avoid separation of the material in the core layer in order to give an improved density profile for particleboard.
A new forming machine for particleboard to increase capacity with the same high board quality is currently under development in Texpan’s R&D department. Other new products include an OSB storage and dosing bin for wet flakes and one for dry flakes. German complete panel line machinery maker Siempelkamp today owns 40% of CMC Texpan, having added 15% of the company to its existing holdings last year. Thus, as you might expect, a lot of business comes from Siempelkamp main contracts. However, CMC Texpan is an independent company and still obtains many contracts by direct contact with the panel manufacturers. It also supplies forming systems to customers with Dieffenbacher presses, for example PT Kutai Timber, Indonesia, which chose to have CMC Texpan forming. As mentioned earlier, Romania is important to CMC Texpan – and another Italian company. Mr Zoppetti informs me that he owns 50% of a company there producing components for CMC Texpan. The other 50% of the equity in Cosmec of Cluj Napoca, Romania is owned by friend and complementary business owner Roberto Moroni of Trasmec. Trasmec is a specialist manufacturer of conveying systems often used with CMC Texpan’s equipment.
Dimeco is the production arm of the holding company Cosmec, and it manufactures components for Texpan’s bunkers, forming machines, hammer mills and other equipment which is delivered to Colzate for assembly into the final machines. Similarly, Dimeco produces components for Trasmec’s belt and screw conveyors, while about 10% of Dimeco’s production is for third party companies in the general engineering sector. "Dimeco provides additional manufacturing capacity for us and a saving of up to 30% on the cost of production in Italy because labour costs are so much lower," says Mr Zoppetti. "We have over 7,000m2 of workshop there, with cranes and automated machinery, and we employ 85 people." Mr Zoppetti also intends in the future to increase the amount of ‘lower-tech’ components which can be manufactured locally to the customer’s panel mill, in order to reduce costs, as the company has already done with its dryer components. This is one of the best ways for us – and the customer – to save money," he says.
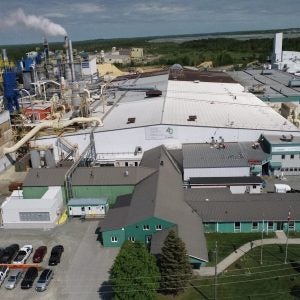