The mill is located on the banks of the Kettle river near the mouth of a scenic canyon and was established about 40 years ago during particleboard’s first growth cycle. The initial product was industrial board, but in later years management saw the value of niche products and gradually switched to door core. Chairman and CEO Bruce Welch bought the mill. A huge high-pressure single-opening Becker & van Hüllen press, one of few still in service, serves the number 2 line. But number 1 line has an impressive new forming system installed under less-than-ideal conditions, making that line the star. Operations director Peter Metcalf said the 30-year-old existing former was "totally worn out. It collapsed as we removed it".
Canpar went to a wider mat with installation of the new Metso blender and screen. This all resulted in a 3% production increase, along with better forming accuracy and improved board qualities. Plenty of pre-planning went into the switchover, with an eight-person team organised for the job so as to minimise downtime. They worked around the clock during the eight-day shutdown after which operations resumed, with the mill back to full capacity in two or three days. Mr Metcalf said Terry McSweeney of Westec did the drawings and was at the mill for the entire installation. "It was nice to have the resource on the site," he said. "And we had the expertise of Metso here.
"It was quite a feat to get that equipment into the building, even disassembled." In the tight quarters, they had to raise the equipment ahead and behind the former, tie it to the roof, bring the former in, and then lower the existing equipment back into place. Manufacturing vice president Randy Johnson, a 30-year veteran of the wood products business, said: "It was a very artful task to shoehorn all that in. The new former has been extremely reliable. I don’t think we’ve had more than nine hours of downtime from it in more than a year". Forming accuracy enables high-quality panels at low densities, while maintaining other standards. Another advantage is self-cleaning rollers. Forming along the length of the line is quite consistent, he said. The system uses a weigh scale in the forming bin, providing instant information about bin flow. At the same time as the new former, Canpar installed a new Carmanah screen to handle the increased volume.
Mr Metcalf said: "We’re the largest door plant in North America and possibly the world. We have a niche. The only industrial board we produce is for our cover sheets". Mr Johnson said his mill’s two major competitors produce perhaps half of his output. "We’re absolutely focused. We’re sold out in North America," he declared. The mill has 123 employees with 91 in production and maintenance and is heavy to value-added business, which tends to be labour-intensive. They produce 237 products in 11’8in and 13’4in, with some 11’2in. Up to one million lock blocks are included in a typical week’s production. These are concealed particleboard blocks glued to the insides of hollow-core doors to provide support for lock sets. All of Canpar’s raw material is softwood sawmill residues, except for wood from one pulp mill. The plant’s raw material supply (chip undersize, planer shavings and sawdust) comes from a 150km radius of the mill. The closest supplier is the Pope & Talbot sawmill just across the street. It is a mixture of pine, fir, spruce and hemlock.
Grand Forks has a fairly mild and dry climate and the wood supply is stored outside, which does result in somewhat higher moisture for the dryers. Both the mill’s two lines draw from a common source. Bauer machines refine the material. Line 1, the improved line with the new Metso Classiformer, has two Bison drum dryers for a second pass. The material, 12 tons per hour, feeds across an Imal weigh-belt and two Carmanah screens to dry storage. A Coen burner fired with sander dust heats the dryers and pre-dryer, serving both Bison drum dryers. Imal/Pal blenders introduce Hexion resin. The mat is trimmed and proceeds to the DeMets 72in roller belt pre-press, then through a Bunting metal detector to the charging rack through company-built trim saws and on to the DeMets 64x120in eight-opening hot press. Refurbished Dieffenbacher platens were added in 1996. A GTS DH-V 10/40 gas-fired boiler heats the press to a normal pressing temperature of 450ºF. Normal pressing time for 11’8in board is 3 minutes 10 seconds. After passing through a cooling chamber the panels go to a shop-built stacker.
Schwabedissen saws trim the panels. All output is sanded after two days of warehouse conditioning. Line 2 employs a Bison 9x45ft rail forming station feeding a Becker & van Hüllen 9x45ft single-opening pre-press heated to 2500F which, in turn, feeds a Becker & van Hüllen 9x45ft single-opening press heated by a gas-fired Cleaver Brooks 750-93 unit. The press has a water hydraulic ram system to produce an extremely high 4,000psi.
The Imal trim line has two 108in edge trim saws, two centre long-cut 28x60in splitter saws, and 12 cross-cut saws, 48x120in. The mill produces standard thicknesses of 11’8in, 11’2in, 15’8in, 111’16in, 13’4in, and 21’4in, cut to almost any size. Edge-gluing produces long panels to be cut to any length. The plant has five thousand ft2 of raw storage and another five thousand ft2 of dry storage. The product is SCS certified. The mill ships 25 rail cars and 25 trucks of panels weekly throughout North America. A one-locomotive short-line railroad owned jointly by Canpar and adjoining Pope & Talbot links the mills with the main Burlington Northern railroad for product shipments.
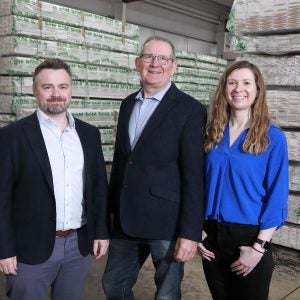