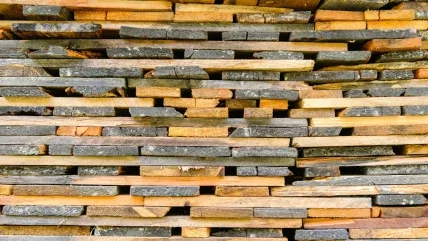
Introduction
Inflation, the gradual increase in prices of goods and services over time, poses a significant challenge for many industries, including the wood-based panels manufacturing and processing sector. This industry, which includes the production of plywood, particleboard, and medium-density fibreboard (MDF), is particularly susceptible to inflation due to its reliance on raw materials, energy, and transportation costs. This article explores the impact of inflation on the wood-based panels industry, examining the factors driving cost increases and discussing strategies for mitigating these effects.
The impact of inflation on raw material costs
One of the most direct effects of inflation on the wood-based panels industry is the increase in raw material costs. Wood, the primary raw material for this sector, has seen significant price volatility in recent years. Several factors contribute to this volatility:
- Supply Chain Disruptions: The COVID-19 pandemic led to significant disruptions in global supply chains, impacting the availability and cost of timber. Lockdowns, port closures, and labour shortages resulted in reduced timber supply, driving up prices.
- Environmental Regulations: Stricter environmental regulations and sustainable forestry practices have reduced the availability of timber. While these regulations are crucial for environmental conservation, they also contribute to higher costs for manufacturers.
- Increased Demand: The surge in home improvement projects during the pandemic increased demand for wood products, further exacerbating supply constraints and pushing prices higher.
The combination of these factors has led to a sharp rise in timber prices, directly impacting the cost structure of wood-based panels manufacturers. As raw material costs increase, manufacturers face the challenge of maintaining profitability without significantly raising prices for end consumers.
Energy costs and inflation
Energy is another significant cost component for the wood-based panels industry. Manufacturing processes such as drying, pressing, and finishing require substantial amounts of energy, typically derived from electricity and natural gas. Inflation in energy prices can therefore have a profound impact on production costs.
- Volatile Energy Prices: Energy prices are subject to fluctuations due to geopolitical tensions, supply-demand imbalances, and policy changes. Recent trends, such as the transition to renewable energy sources and the geopolitical instability in oil-producing regions, have led to increased energy costs.
- Carbon Pricing: Many countries are implementing carbon pricing mechanisms to reduce greenhouse gas emissions. While this is a positive step towards mitigating climate change, it also increases energy costs for manufacturers reliant on fossil fuels.
- Energy Efficiency Investments: To counter rising energy costs, manufacturers are investing in energy-efficient technologies and processes. While these investments can lead to long-term savings, they require significant upfront capital, adding to short-term financial pressures.
Labour costs and inflation
Labour costs in the wood-based panels industry are also influenced by inflation. Wage inflation, driven by factors such as minimum wage increases and labour shortages, directly impacts operating costs. The industry has been grappling with several labour-related challenges:
- Skilled Labour Shortages: The wood-based panels industry requires skilled labour for various manufacturing processes. However, there is a shortage of skilled workers, partly due to an ageing workforce and a lack of new entrants into the field. This scarcity drives up wages as companies compete for limited talent.
- Increased Labour Costs: Inflationary pressures lead to higher wage demands from workers. In regions with strong labour unions, collective bargaining can result in significant wage increases, adding to the cost burden for manufacturers.
- Automation and Training: To address labour shortages and rising wages, many manufacturers are turning to automation. Investing in automation technology can enhance productivity and reduce reliance on manual labour. However, the initial investment in automation and the need for specialised training can be costly.
Transportation and logistics costs
Transportation and logistics are critical components of the wood-based panels supply chain. Inflation in transportation costs, driven by fuel price increases and logistical challenges, further impacts the industry.
- Fuel Price Volatility: Fuel prices are subject to significant fluctuations due to geopolitical events, supply-demand dynamics, and policy changes. Rising fuel costs directly impact transportation expenses, increasing the cost of delivering raw materials and finished products.
- Supply Chain Disruptions: The COVID-19 pandemic highlighted the vulnerability of global supply chains. Disruptions in transportation networks, port congestion, and container shortages have led to increased logistics costs and longer delivery times.
- Optimising Logistics: To mitigate rising transportation costs, companies are exploring logistics optimisation strategies, such as consolidating shipments, improving route planning, and leveraging digital technologies. These measures can enhance efficiency and reduce costs but require investment in technology and infrastructure.
Mitigation strategies for inflationary pressures
While inflation poses significant challenges, wood-based panels manufacturers can adopt various strategies to mitigate its impact:
- Cost Management and Efficiency: Manufacturers can focus on improving operational efficiency to reduce costs. This includes optimising production processes, reducing waste, and implementing lean manufacturing principles.
- Strategic Sourcing: Diversifying sources of raw materials can help mitigate supply chain risks and reduce dependency on a single supplier. Developing long-term relationships with suppliers and exploring alternative materials can provide more stability in raw material costs.
- Investment in Technology: Investing in advanced technologies, such as automation, digitalisation, and energy-efficient machinery, can enhance productivity and reduce operational costs. While the initial investment may be high, the long-term benefits can outweigh the costs.
- Price Adjustments: While increasing prices is often a last resort, it may be necessary to maintain profitability. Companies can adopt a value-based pricing strategy, where prices reflect the value delivered to customers rather than simply covering costs.
- Hedging and Financial Instruments: Using financial instruments such as futures contracts and hedging can help manage price volatility in raw materials and energy costs. These instruments provide a level of predictability and stability in cost management.
- Sustainable Practices: Adopting sustainable practices, such as using certified timber and reducing carbon emissions, can not only enhance a company’s reputation but also lead to cost savings in the long run. Sustainable practices can open up new markets and attract environmentally conscious consumers.
The role of government and industry associations
Government policies and industry associations play a crucial role in addressing inflationary pressures. Policymakers can implement measures to stabilise prices and support the industry through:
- Subsidies and Incentives: Providing subsidies and incentives for energy-efficient technologies and sustainable practices can help offset some of the costs associated with inflation.
- Infrastructure Development: Investing in transportation and logistics infrastructure can reduce bottlenecks and improve supply chain efficiency, thereby lowering costs for manufacturers.
- Training and Education Programmes: Supporting training and education programmes to develop skilled labour can address workforce shortages and reduce wage inflation.
- Trade Policies: Implementing favourable trade policies and reducing tariffs on raw materials can help stabilise prices and ensure a steady supply of inputs for the industry.
Industry associations can also play a vital role by advocating for favourable policies, providing market insights, and facilitating collaboration among industry players to address common challenges.
Conclusion
Inflation presents a multifaceted challenge for the wood-based panels manufacturing and processing industry. Rising costs of raw materials, energy, labour, and transportation require manufacturers to adopt strategic measures to maintain profitability and competitiveness. By focusing on cost management, strategic sourcing, technological investments, and sustainable practices, companies can navigate the complexities of inflation and position themselves for long-term success. Additionally, supportive government policies and active industry associations can provide the necessary framework for the industry to thrive amidst inflationary pressures.